Königsdisziplin der Instandhaltung?
Philip Vodopiutz (IPN Intelligent Predictive Networks GmbH)
Daten im Zentrum: zukünftige Anlagenzustände voraussagen
Die zustandsorientierte und die vorausschauende Instandhaltung gelten als Shooting-Stars der Instandhaltungsstrategien: Sie treten immer stärker neben reaktive und präventive Instandhaltungsstrategien und werden in erster Linie durch die zunehmende Datenzentriertheit am Shop-Floor sowie durch neue analytische Verfahren ermöglicht.
Condition Monitoring (Zustandsüberwachung) dient zur Überwachung des momentanen Maschinenzustands (siehe dazu Beitrag „Strategisches Condition Monitoring” auf Seite 15»). Dabei werden Sensoren zur Erfassung von Messwerten und Prozesszuständen eingesetzt und ihre Messwerte auf Abweichungen von der Norm überwacht.
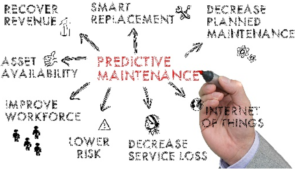
Im Gegensatz dazu liegt der Fokus von Predictive Maintenance auf dem zukünftigen Zustand der Anlagen. Es werden kontinuierlich alle verfügbaren Messwerte und relevanten Ereignisse (beispielsweise Störungen) der Anlage gesammelt und durch computergestützte, statistische Methoden der zukünftige Zustand bewertet.
Predictive Maintenance: Wie es in der Praxis funktioniert
Die Vorstellung, man müsse nur genügend Daten sammeln und eine „Künstliche Intelligenz“ gäbe dann die Antworten auf alle Fragen, hält sich beständig. In der Realität ist die Einführung von Predictive Maintenance harte Arbeit und viele Projekte scheitern schon bei der Datenerzeugung und -Sammlung.
Datensammlung
Für Predictive Maintenance gilt „Garbage in – Garbage Out“. Fehler bei der Datensammlung verursachen ein Vielfaches an Kosten bei der Verwertung. Zur Einführung von Predictive Maintenance müssen zuerst die richtigen Fragen formuliert werden, um zu definieren, welche Daten in welcher Qualität gesammelt werden sollen. Dabei wird darauf geachtet, die gesamte Anlage über die Daten abzubilden und bisher unbekannte Abhängigkeiten zu berücksichtigen.
Prognosemodelle
Relevante Störungen an Anlagen treten selten auf, daher sind reine Machine Learning Ansätze zur Entwicklung von Prognosemodellen in der Regel ungeeignet. Prognosemodelle werden durch Datenanalysten gemeinsam mit Anlagenexperten auf Basis der gesammelten Daten und dem Fachwissen der Experten entwickelt.
Adaptive Modelle
Predictive Maintenance basiert auf einer kontinuierlichen Datensammlung. Dadurch können sich Modelle an neue Produktionsgeschwindigkeiten, Rohstoffe oder andere Veränderungen anpassen.
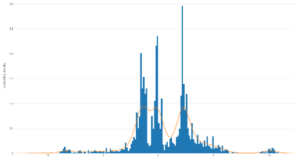
Ergebnisse
Ziel von Predictive Maintenance ist die Prognose sowie in weiterer Folge die gezielte Planung oder Verhinderung von Anlagenausfällen. Zum Beispiel kann der Wartungsbedarf einer Kühlanlage einen Monat vor der Störung punktgenau prognostiziert werden. Oder es können Einstiegssysteme von Zügen rechtzeitig außer Betrieb genommen werden, um ein Blockieren in Offenlage in einer Station zu verhindern.
Quick-Wins
Die Datenbasis für Predictive Maintenance erlaubt detaillierte Analysen von Zusammenhängen in den Anlagen und ermöglicht damit viele Optimierungen. Energieeffizienz kann in Abhängigkeit der Produktqualität betrachtet, Störungstreiber identifiziert und Analgenoptimierungen zielgerichtet durchgeführt werden.
Ein Anwendungsbeispiel dazu finden Sie hier »