Herausforderungen, Anwendungen und Nutzen von digitale Zwillingen in der Instandhaltung
Georg Güntner (Salzburg Research)
Die Rolle von Digital Twins in der Instandhaltung
Motivation
Das renommierte amerikanische Marktforschungsunternehmen Gartner hat 2017 die Digital Twins zu einem der zehn bedeutendsten technologischen Trends erklärt ([Gartner2017]). Auch die Hannover Messe 2018 widmete dem Thema Digital Twin einen Schwerpunkt ([Han2018a], [Han2018b]).
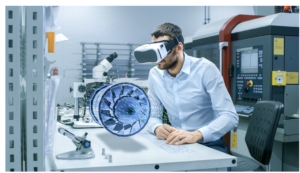
(© Salzburg Research, Fotolia.com, Gorodenkoff)
Das sollte Anlass geben, sich in einem Bericht über die digitale Transformation der Instandhaltung auch mit den Herausforderungen und potenziellen Anwendungen von Digital Twins in der Instandhaltung auseinanderzusetzen. Oder etwa nicht? Haben digitale Zwillinge überhaupt einen Bezug zur Instandhaltung? Bevor wir uns mit diesen Fragen auseinandersetzen, vorab eine Definition des Begriffs.
Definition
Eine allgemeine Definition des Begriffs findet sich im Gabler Wirtschaftslexikon: „Ein digitaler Zwilling (englisch ‚Digital Twin‘) bezieht sich auf ein computergestütztes Modell eines materiellen oder immateriellen Objekts, welches für verschiedene Zwecke verwendet werden kann.“ ([Spring2017]).
Digital Twins für industrielle Assets
In die industrielle Fertigung übertragen treten an die Stelle der materiellen Objekte Maschinen und Anlagen (industrielle Assets) sowie deren Komponenten, aber auch Werkzeuge, Ersatzteile und die erzeugten Halb- und Fertig-Produkte. Die computergestützten Modelle bilden die geometrischen, kinetischen und/oder Zustandsinformationen dieser Objekte ab. Immaterielle Objekte sind im industriellen Kontext beispielsweise die Produktions- und Instandhaltungsprozesse.
Sensoren, Lebenszyklus und die Nutzung der Daten
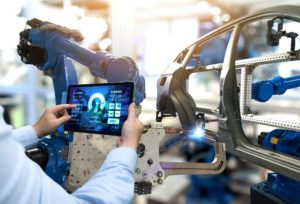
(© Salzburg Research, Fotolia.com, zapp2photo)
Digitale Zwillinge kann man sich als digitales Abbild von industriellen Anlagen in einem computergestützten Modell vorstellen. Sie verwenden Sensoren, um die Betriebszustände und -prozesse von industriellen Assets über ihren Lebenszyklus hinweg digital zu erfassen. Die gesammelten Daten werden in einem Datenhaltungssystem gespeichert. Dabei kommen klassische Datenbanksysteme oder Cloud-Lösungen zum Einsatz. Digital Twins bilden daher eine aktuelle digitale Kopie der Zustände und Eigenschaften von industriellen Assets ab. Sie unterstützen damit potenziell die Überwachung (Monitoring), Diagnose und Vorhersage des Betriebes von Anlagen, indem sie die gesammelten Daten visualisieren, analysieren und zukünftige Zustände und Ereignisse prognostizieren können ([Wiki2018]).
Der Nutzen von Digital Twins für die Instandhaltung
Zukunftsorientierte Instandhaltungsstrategien
Allein aus diesem ersten Denkansatz, der sensorischen Erfassung von Zustandsinformationen, lässt sich die Frage nach dem Bezug von digitalen Zwillingen zur Instandhaltung eindeutig beantworten: Instandhaltungsprozesse profitieren deutlich vom Konzept des digitalen Zwillings, indem sie die Zustände und Betriebsparameter von Maschinen und Anlagen über längere Zeit erfassen und damit instandhaltungsrelevante Entscheidungen und Handlungen ableiten ermöglichen.
Erfüllen nicht auch Condition Monitoring Ansätze einen ähnlichen Zweck? Im Grunde ja, aber wir haben bisher nur einen Aspekt der digitalen Zwillinge betrachtet. Aber schon dieser Aspekt zeigt uns, dass wie digitale Zwillinge für die Anlagenüberwachung, die Ermittlung von Kennzahlen, die frühe Erkennung, Vorhersage und gänzliche Vermeidung von Schadensfällen und Stillständen verwenden können. Damit lassen sich nicht nur zukunftsorientierte Instandhaltungsstrategien (zustandsorientierte bzw. voraussagende Instandhaltung, vgl. [Guen2015c]) umsetzen, sondern es bieten sich auch neue Geschäftsmodelle (beispielsweise Remote Services und Predictive Maintenance Services).
Die vielen Gesichter des „Digital Twins“
Ihr volles Potenzial spielen digitale Zwillinge aus, wenn sie die über eine reale Anlage verfügbaren digitalen Informationen intelligent verknüpfen und dadurch zu einem für den jeweiligen Anwendungsbereich vollständigeren digitalen Abbild der Anlage kommen. Ein Digital Twin kann also viele verschiedene Gesichter haben. Allein die Anwendung und der geplante Nutzen entscheiden, welcher Ausschnitt des gesamten digitalen Abbilds umgesetzt wird.
Digitale Zwillinge als fachübergreifender Ansatz
Die Informationen, die das digitale Abbild eines industriellen Assets formen, kommen aus verschiedenen Fachbereichen (siehe Abbildung 3):
- dem Produktionsplanungs- und Steuerungs-System (ERP-System),
- den Supply-Chain-Management-Systemen,
- den Konstruktions- und Entwicklungsabteilungen mit den dort eingesetzten CAD- und Simulations-Systemen
- den Instandhaltungsabteilungen mit den dort eigesetzten CMMS-Systemen,
- den Produktionsabteilungen und den dort eingesetzten Betriebsdatenerfassungs- und SCADA-Systemen,
- den Dokumentationsabteilungen,
- den Asset Management Abteilungen
- den IT-Abteilungen und den dort verwalteten Datenhaltungssystemen einschließlich der Cloud-Plattformen
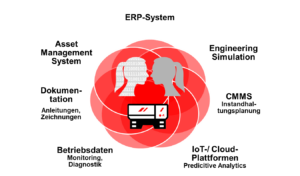
Das Puzzle der Daten und Informationen eines digitalen Zwillings
Die Liste der möglichen/relevanten Informationen und ihr Bezug zur Instandhaltung umfasst dabei:
- Die Stammdaten der Anlage: z.B. die beschreibenden Daten eines technischen Platzes, die „Verwaltungsschale“ von RAMI 4.0 (vgl. [BMWi2016], [DIN91345-2016]), dazu gehören auch Ortskoordinaten (für Weg- und Lagebeschreibung) und kennzeichnende RFID-Codes (für die Identifikation von Anlagen und Bauteilen), usw.
- Die Anlagenstruktur: z.B. aus dem CAD-System beim Hersteller, dem ERP-System, dem CMMS-System, usw.
- Instandhaltungspläne und die Dokumentation von Instandhaltungsmaßnahmen: üblicherweise im CMMS verwaltet.
- Die Betriebs- und Prozessdaten als Basis für Monitoring, Diagnostik und Predictive Maintenance: Dies entspricht dem eingangs erwähnten Aspekt der Sensorik, kann jedoch um weitere Informationen ergänzt werden (Position, Bewegung, Formen, usw.).
- Die 3D-/CAD-Modelle der Anlage: diese unterstützen neben der kinetischen Simulation auch Schulungsmaßnahmen und Instandhaltungsanleitungen mit Augmented Reality und Virtual Reality (z.B. für Assistenzsysteme).
- Die Anlagen-Dokumentation: CAD-Zeichnungen, Betriebs- und Wartungsanleitungen (auch audiovisuelle Aufzeichnungen über die Durchführung von Instandhaltungsmaßnahmen), Prüfbescheide, Zertifikate, usw. Dies ist die Domäne von Dokumenten-Verwaltungssystemen (DMS)
- Dynamische Modelle der Anlage für Simulationszwecke (z.B. für virtuelle Steuerungskonzepte und für Tests in der Inbetriebnahme-Phase).
- Informationen zum Lebenszyklus: Änderungsdokumentation, historische Information über Störmeldungen, Stillstände und Instandhaltungsmaßnahmen.
Gesamtkonzept für den Digital Twin
Die Integration und Beherrschung der Vielfalt der in einem Digital Twin zusammenlaufenden Informationen und Daten ist eine durchaus komplexe Aufgabe, der sich Software-Anbieter (z.B. ERP-Lösungen, IoT-Plattformen), Systemintegratoren, Anlagen-Herstellern und Service-Anbietern aus verschiedenen Blickwinkeln annähern. Die Unternehmen sind bei der Wahl der richtigen Digitalisierungsstrategie und ihrer Partner durchaus gefordert.
Aber es ist nicht die Instandhaltungsabteilung allein, die das Konzept und die Implementierung einer Digital Twin Lösung beauftragen muss. Vielmehr geht es um ein Gesamtkonzept für das digitale Abbild eines industriellen Assets, an dem die IT-, Engineering-, Produktions-, Instandhaltungs- und Asset Management Abteilungen gleichermaßen – und oft über die Unternehmensgrenzen (z.B. Anlagen-Hersteller, Service-Anbieter) hinaus – beteiligt sind. Die Aufgabe der Instandhaltungs-Abteilung besteht darin, dafür zu sorgen, dass ihre wichtigsten Anliegen in einer Digital Twin Implementierung berücksichtigt werden: Dazu gehören das Monitoring (z.B. Instandhaltungs-Dashboards), die Unterstützung fortschrittliche Instandhaltungsstrategien (nutzungs- oder zustandsorientierte Instandhaltung), komplexe Prognostik (z.B. Predictive Maintenance), die Verfügbarkeit von Dokumentation und multimedialen Anleitungen, AR-/VR-Assistenzsysteme für die Instandhaltung (vgl. Abbildung 1).